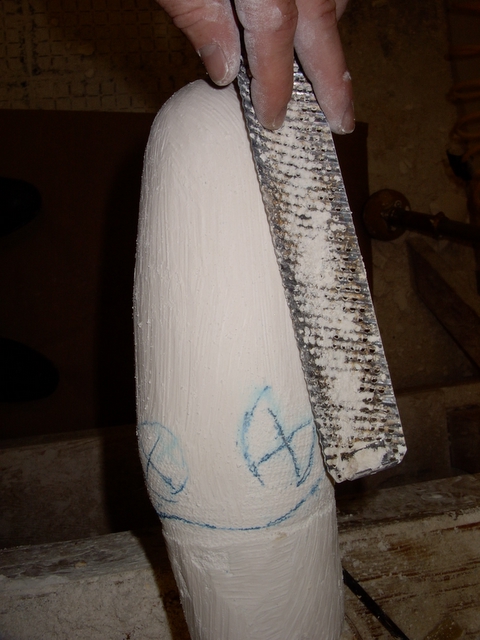
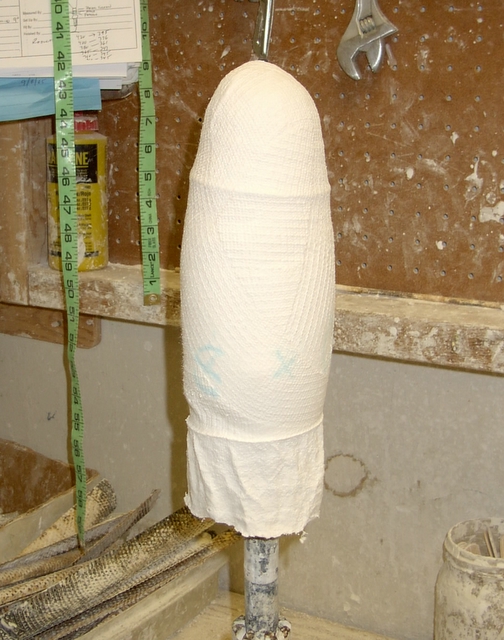
I still haven’t got my prosthetic hand yet, it’s been a challenge for Richard at Hanger to get a test socket to fit. My stump is a bit bulbous, which, as you can imagine, makes it a challenge to get a socket to go over the bulge in the middle yet still fit snuggly to the stump.
It was third time lucky last week though, Richard successfully created a socket that fitted well. Now he will turn this test socket into a real one made from carbon fiber and then I can start experimenting with the hand attachments to see how they work for me, I’m quite excited to finally get to try something out and see what difference it makes.
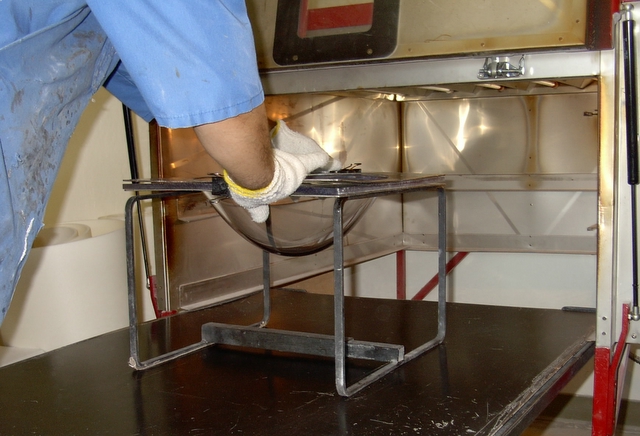
Richard kindly took some photos of the process of making the test socket. The first one on the left is the initial mould taken from the cast he made of my arm, it’s pretty rough and has to be sanded down and smoothed out before they can make the socket from it. As you can see they just use a normal file to get rid of the imperfections and to reduce the size of the mould by 3-5%…this is where the skill comes in to reduce the size but not to make it too small that the resulting socket won’t fit. In my case, for the third test, Richard didn’t reduce the size of the mould at all, instead, when he took the cast of my arm he shaped the tissue in my arm while it set.
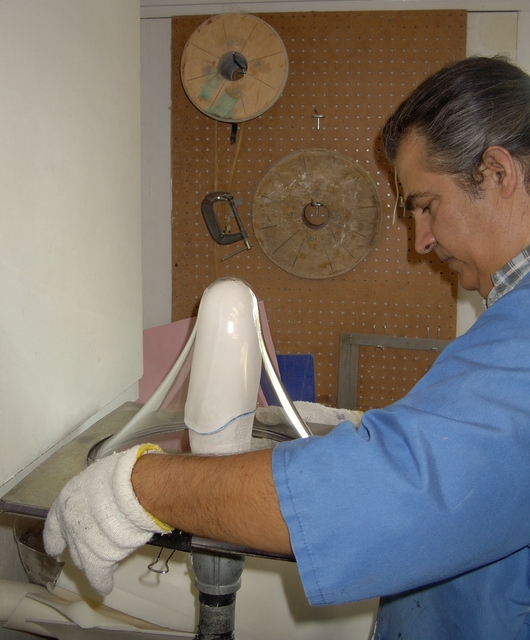
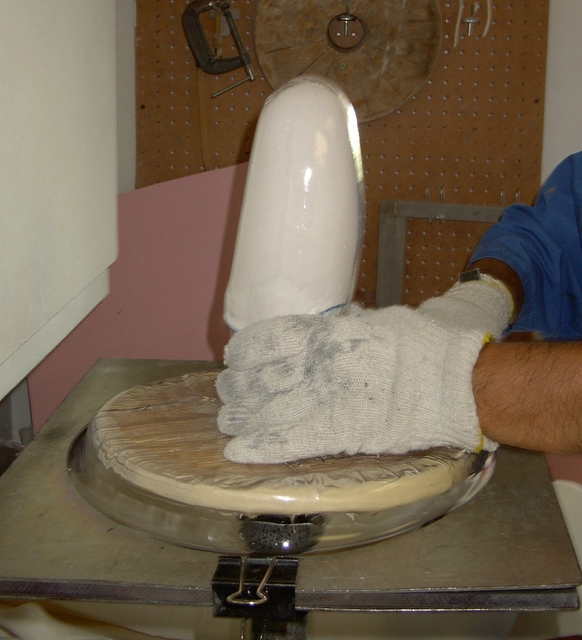
In this next shot you see them heating the plastic sheet ready to make the socket, notice how it’s bowing down. Then they shape the sheet around the mould and finally apply the vacuum to suck all the air out and create the final result.
Leave a Reply