Last week I visited Hanger Hanger Orthopedic again, it took a while to sort out the insurance paper work with Kaiser but it’s all systems go again.
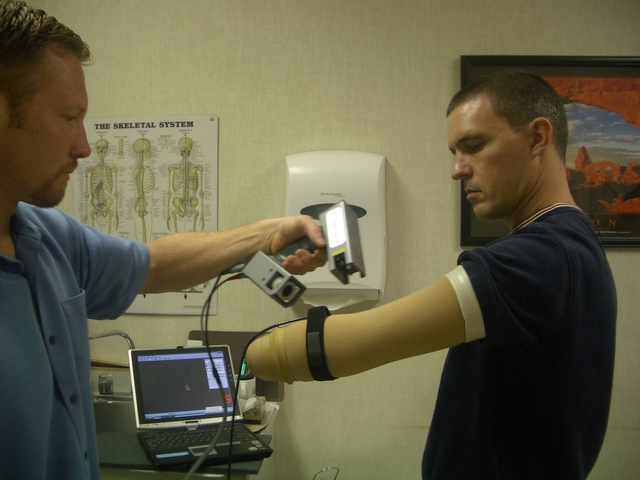
My first visit on Wednesday was to take a molding of my arm from which they’d be able to make a test socket. A socket is the part of the prosthetic that fits onto my arm to which the hand, or other such device, is attached.
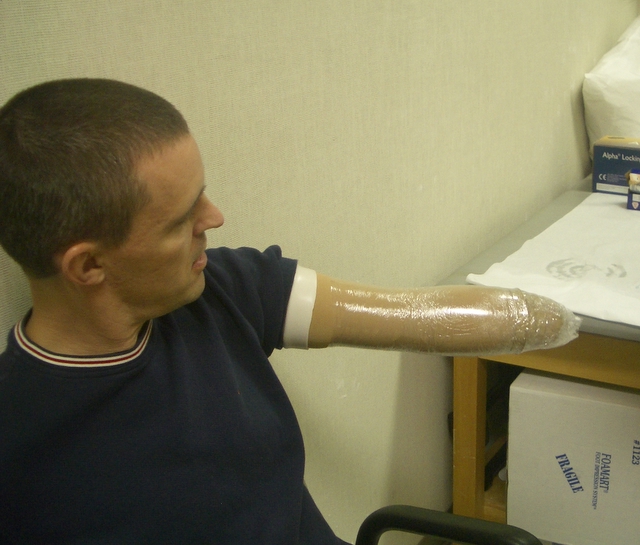
The first step was to get a gel sleeve onto my arm. This is a bit like a neoprene sleeve (except it’s silicone) that you roll onto your arm; you should be able to see it in the picture. Richard, the guy from Hanger, then used a laser to scan my arm and create a 3D image on his computer. It was pretty cool to see the image building up as he moved the laser over my arm, but, unfortunately due to software issues he couldn’t save the scan…we’ll have to play with that again another day.
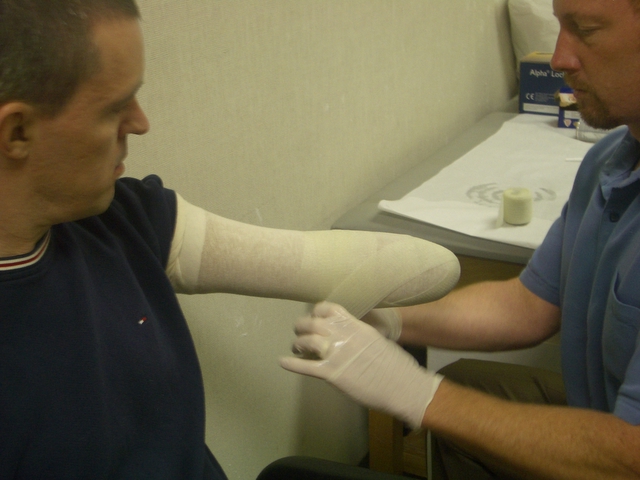
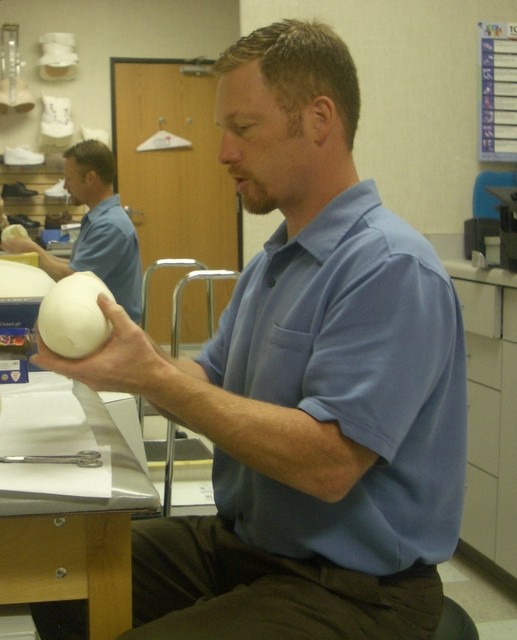
The scan would have been a useful record of my arm and whilst it’s possible to make a socket from it, Richard prefers to still take a molding himself using fiberglass bandages. He first covered my arm in cellophane and then a cloth sock, he wetted the bandages and wrapped my arm, molding it carefully to fit its shape. After a couple of minutes it was dry and the cloth sock was pulled off along with the mold. From this Richard would be able to make a clear plastic, test socket.
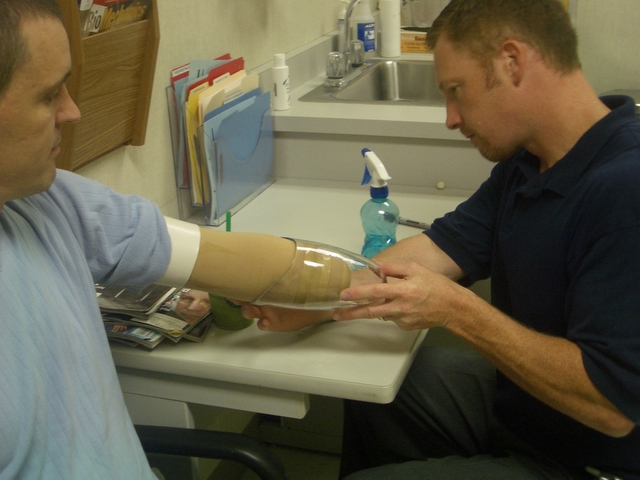
I was back at Hanger on the Friday (they work quick) to see how the test socket fitted. Unfortunately despite several adjustments the socket was just a little bit too small. It was interesting however to see how the socket worked, using a vacuum to stay on my arm.
So it was back to square one, Richard took another molding of my arm (he had to break the previous one when he made the casting). My arm is a little bulbous in the middle, which makes it tricky to make a socket that can go on, but still be tight and fully make contact with the arm. We’ll see if he has better luck next time.
Leave a Reply